Blogs
Services
Balancing QA and QC: The Importance of Quality Assurance Audits
Nov. 20, 2024
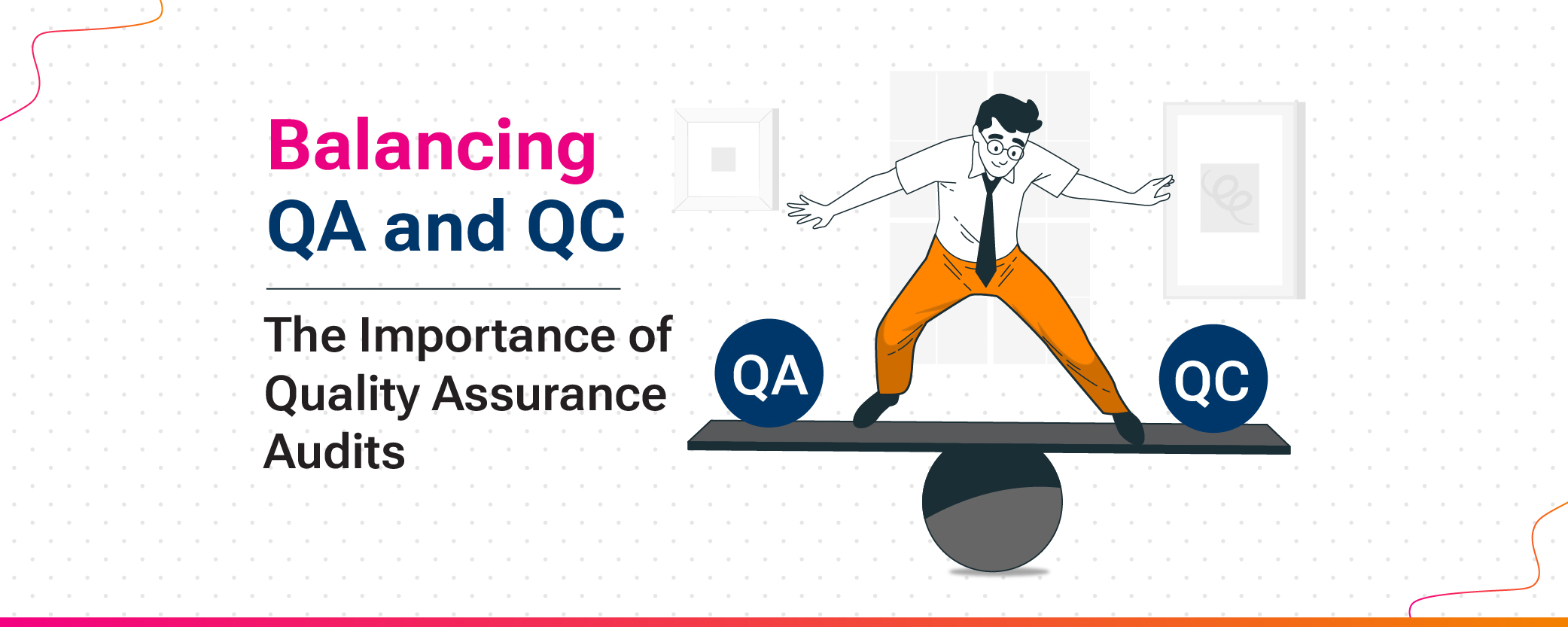
Be it a product or a service, when it comes to its development, there are multiple stages involved. At each stage, the product or services become better than before. However, with the progression of each stage, the challenge is to maintain the quality. This issue can be resolved through quality management, which is done in two steps- quality assurance and quality control. Even though it is a common misconception that they are the same, both these processes are complementary. So, in this blog, we will understand the difference between quality assurance and quality control and get to know how Quality Assurance Audits help to reduce defects in your business.
Quality Assurance Vs. Quality Control
Quality is one of the most crucial pillars of a successful business and cannot be neglected in the slightest bit. Hence, quality assurance and quality control both play an equally important role in maintaining the standards of your products and services. However, they both ensure quality in a different way. So, let's understand the key difference between the two in order to understand their importance better.
Firstly, quality assurance is a proactive approach as one has to actively set up processes and systems in order to ensure that the product that is being built already has good quality. So, it helps to set up a high standard from the beginning itself. In contrast, quality control is more of a reactive step in which one has to inspect the product thoroughly and then get rid of any issues that may have come up during the development process.
In other words, QA is about preventing problems, while QC helps to find and fix them. Moreover, QC also ensures that all the issues get resolved before the products reach the customers. Meanwhile, QC ensures that the processes are well-designed to prevent any errors in the first place.
In short, QA and QC are not interchangeable, as both have different functions and roles to play in the quality management system. Hence, relying on QC or QA alone cannot ensure quality, and they must be paired together. Not only will it help to produce more high-quality products, but it will also be more reliable.
Principles of Quality Assurance
The foundation of creating reliable, high-quality products and services is formed by the Quality Assurance principle. Besides, they ensure that the processes are designed to prevent errors and meet customer expectations. So, what are these principles? Let's find out.
Customer Focus
Quality revolves around your customer's expectations. So, meeting or exceeding your customer's expectations is a core QA principle. It helps to design processes in a way that delivers products aligning with what customers need.
Leadership
A clear vision can be achieved only under strong leadership. It helps to get defined goals and consistent quality standards across your company. Hence, as a leader, you must foster a culture of quality and empower your employees to contribute effectively.
Process approach
QA always puts an emphasis on managing activities as interconnected processes. It helps optimize workflows and identify inefficiencies while enhancing productivity.
Engagement of people
Maintaining quality is the responsibility of each team member. Hence, employee involvement must be encouraged, and proper training must be given. Besides, it's also important to recognize contributions if you want a successful implementation of QA.
Improvement
If you want to stay competitive in your industry, then you need to improve continuously. Evaluate and refine your processes for sustained quality and adaptability.
Relationship management
What Should You Choose: QA or QC?
Both quality assurance and quality control are essential, but can you decide which one is more important? While QA focuses on creating processes and standards that ensure safe and efficient operations, QC makes sure that the final product meets the set standards.
Quality assurance audits help to increase the quality of the development processes. It also reduces the workload during quality control as the error becomes lesser due to proper supervising. Quality assurance audits ensure that processes and products meet established standards, enhancing overall quality and reliability. They identify gaps, reduce errors, and improve efficiency, leading to higher customer satisfaction. Regular audits also foster continuous improvement, compliance with regulations, and better risk management, ultimately boosting the organization's credibility and competitiveness.
Conclusion
In simple words, neglecting either QA or QC can lead to inefficiencies and customer dissatisfaction. Moreover, it also contributes to missed opportunities for growth. Hence, maintaining a balance it's important for high standards and continuous improvements. Moreover, quality assurance audits play a vital role in identifying gaps and refining processes. It also ensures proper compliance and long-term success. Besides, regular quality assurance audits only strengthen the processes but also help you deliver consistent and reliable products and services.
quality assurance is a proactive approach as one has to actively set up processes and systems in order to ensure that the product that is being built already has good quality.